Table Of Content
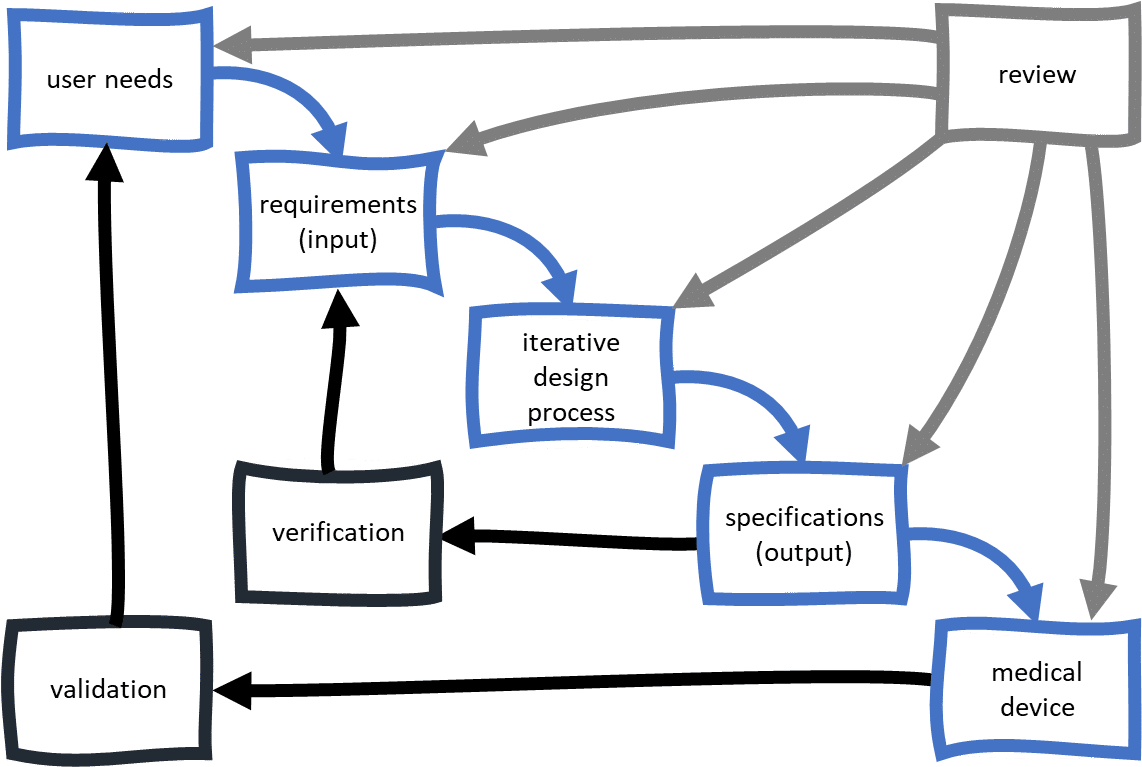
Design Controls began when the FDA authorized the Safe Medical Device Act of 1990 to expand the scope of current Good Manufacturing Practice (cGMP) to impose more control over the development process of medical devices. The intention was to avoid uncontrolled changes during the design process and afford more predictability to ultimately avoid previously unforeseen problems. Formal design reviews are planned and typically conducted at the end of each design stage or phase, or after completion of project milestones. The number of reviews is dependent on the complexity of the design. A single review may be appropriate at the conclusion of the design project for a simple design or a minor change to an existing product.
A novel on design and implementation of hybrid MPPT controllers for solar PV systems under various partial shading ... - Nature.com
A novel on design and implementation of hybrid MPPT controllers for solar PV systems under various partial shading ....
Posted: Thu, 18 Jan 2024 08:00:00 GMT [source]
Design Verification Insight
These production units (maybe the first) are then put in the hands of end users. So all those Design Outputs (the preliminary DMR) need to be converted to the production environment and used by production personnel to assemble devices. Design Outputs have a huge impact on the future state of your medical device. As you establish the Design Outputs, you need to show how these relate and link to the Design Inputs. Do so with a Design Controls traceability matrix (as discussed earlier). There are things like industry standards, regulations, and competitive products that you should also consider when it comes to defining Design Inputs.
Completing Design Changes and the Design History File (DHF)
This is your complete guide to understanding just what Design Controls really means for your medical device product development. If you enjoyed this article, check out our intensive medical device design control training class. Also, if you’re not sure where to start with implementing design controls in your company, we can help. All of these inputs must be documented, reviewed, and approved for adequacy, and you need to make sure that the requirements are complete, clear, and don’t conflict with one another. Basically, design inputs should specify what the design is intended to do but they should avoid specific design solutions. Your product developers play a key role (but not the only one) in developing the design input requirements, regardless of who developed the initial product concept.
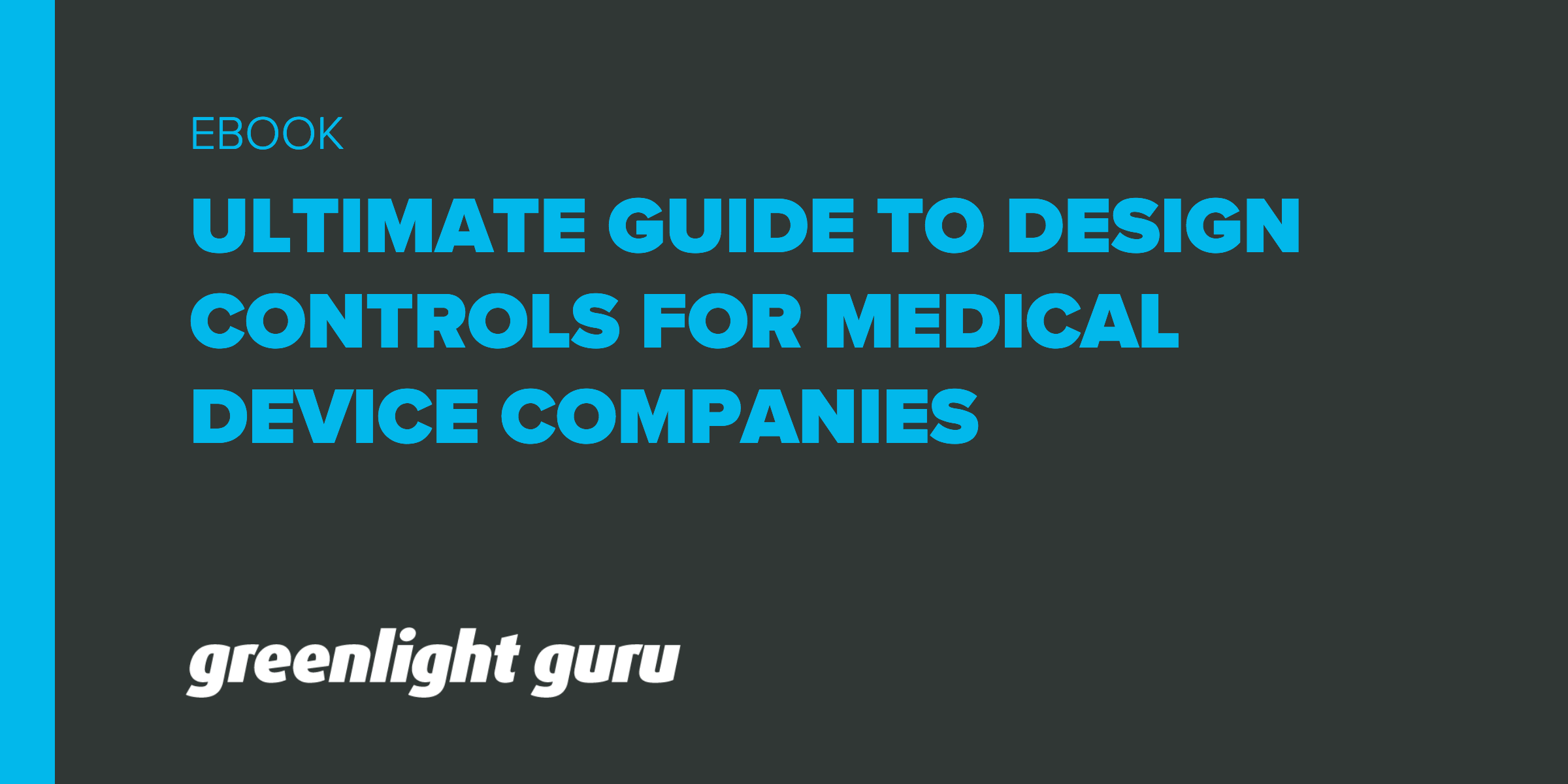
Design Output Insight
Completing Design Validation is an important step in closing the loop on your traceability matrix too. The traceability matrix started with User Needs and ends with Design Validation. If you have been keeping your Design Controls traceability matrix up to date, you have a clear picture of the relationship between your Design Inputs and Design Outputs.
When you get to Design Verification, your goal is to prove your Design Outputs meet the Design Inputs. Design Verification is all about demonstrating you correctly designed your medical device. Remember Design Inputs are the roadmap used to design and develop your medical device. Design Inputs describe everything that is important and required about your medical device. Considering how you will verify will have a profound impact on the content of Design Inputs. You should definitely put thought into how you will prove your medical device will be verified when you define Design Inputs.
It is important to note that Design Controls start with the approval of the design inputs. If a new idea for a medical device is conceived it is beneficial to have a research / concept phase to evaluate technical feasibility. After the company has decided to pursue the project and provides the required funds, resources and staff, Design Controls should start.
How to Make Design Controls More Efficient: Here is a Tested Tool for Design Engineers
With Design Validation, you need to figure out how to prove that your product accomplishes this. Although testing is not the only way to conduct Design Verification. You might also be able to employ inspection and analysis as acceptable methods for Design Verification. All Design Controls must be included as part of a Design Review. As noted, I cannot for certain tell you exactly when to have Design Reviews.
What Is a Design History File (DHF)?
The goal of this Design Transfer Design Review is to make sure everything that is needed for production is ready and done. The end goal of Design Validation is to have objective, documented evidence. If you remember the discussion about User Needs, I shared that sometimes User Needs have a tendency to be a little ambiguous, using words like “easy” and “better”.
As R&D engineers Design Controls impact us mostly during product development (I include changes and modifications to the design in this activity). It is important that product development normally consist of much more than Design Controls. As an example prototypes should be created before Design Controls are started (more on this topic in “Design Controls and Lean”). Note that Device Master Records (DMR) are commonly mixed up with DHF. The DMR is a "recipe" for the device including drawings, specifications, and work instructions, whereas the DHF represents the activities supporting its development. To make matters more confusing there is also the Device History Record (DHR) which is maintained to house all of the records specific to each batch/lot of devices.
Verification testing proves conformance with documented design outputs and inputs, whereas production testing determines whether the unit being tested has been manufactured correctly. Production testing is rarely comprehensive enough to verify the design. Design control is not a “once and done” process – it applies to modifications or improvements to existing designs, or changes to processes.
CQ CAPA management solution uses predictive analytics and intelligence to identify the right issues to solve. The solution supports various methodologies like 8D, 5W-2H, and World Class Manufacturing (WCM). As for timing, the design validation is completed after clinical evaluation is complete. Your clinical evaluation may include a clinical trial but is more likely to consist of safety testing, literature searches, etc. Also, regulators know that it is not always practical to perform clinical studies on finished products, so you are allowed to use prototypes.
This is true for both new developments or changes to existing products. FDA regulations for medical devices are strict, complex and lengthy. Here’s a plain and simple version of design controls for medical device development to help you understand FDA design controls for medical devices. Plus best practices for implementing design controls as productively as possible. Outputs must be comprehensive enough to characterize the device design to allow for verification and validation. Also, design outputs which are essential for the proper functioning of the device must be identified.
Medical device product development should follow a structured, methodical approach with traceability throughout. This is significant because up until this point the “control” of the medical device has been the responsibility of the project team. Once Design Transfer occurs, the control shifts to production resources. As you get into the hands-on, nitty-gritty design and development, you start to identify all the parts and pieces that are required for your medical device. Demonstrating traceability of all your Design Controls throughout the product development process is expected and required.
All about making sure you have proven your medical device meets the requirements you define. It is important that you design and develop a medical device that is safe. FDA, European Commission, Health Canada, and all other regulatory bodies throughout the world will want some assurances that your medical device is safe before you bring the product to market.
This project will be used to evaluate the process, the methods, and the procedures that the firm has established to implement the requirements for design controls. About 20 years later FDA has followed this up with a guideline concerning the implementation of the legislation. Around the same time the ISO was created (based on ISO 9001) due to similar reasons.
Design outputs are the work products or deliverables of a design stage. Examples include, diagrams, drawings, specifications and procedures. The outputs from one stage may become inputs to the next stage. The total finished design output consists of the device, its packaging and labeling, and the device master record. Each manufacturer shall establish and maintain procedures for the identification, documentation, validation or where appropriate verification, review, and approval of design changes before their implementation. The focus of design control is predominantly centered around the type of device, software used, materials required, and manufacturing process.
No comments:
Post a Comment